The motion base is 6 degrees of freedom (DOF) motion queuing device designed for use in real time simulators. The motion system was developed as a cost effective solution for providing motion in 6 DOF. The major system components are the digital controller, motion base assembly and motor unit. The dynamic platform motion is controlled by the six motors coupled through universal joints. The platform provides an area on which the load is mounted. The motion base is designed to sink at a controlled rate to a stable position without electrical power and/or during an abort. The motion system is designed so that it will not reach any kind of unsafe or unstable configuration. In addition to velocity control, position control of each motor to a high level of accuracy is provided. Any position within the stroke range of the motors can be selected. Additional control functions, such as acceleration/deceleration control can also be provided with this system.
Hexapod is a mechanical device that can provide six degree of freedom. As its name indicates hexa means six and pod means structure. It is a six leg mechanical device. There are three linear option of its top plate along X,Y and axis and rotary motion along X,Y and Z axis (Pitch, Roll and Yaw). In a parallel-kinematic multi-axis system, all actuators act directly on a single moving platform. This means that all axes can be designed with identical dynamic properties, thus reducing the moved mass considerably. Hexapods are used for moving and precision positioning, aligning and displacing loads in all six degrees of freedom, i.e., three linear and three rotational axes. Hexapods are widely used for precision positioning, but their workspace is too limited for some applications.
There are some special types of application of electrical motor where rotation of the motor is required for just a certain angle not continuously for long period of time. For these applications, some special types of motor are required with some special arrangement which makes the motor to rotate a certain angle for a given electrical input. For this purpose servo motor comes into picture. The main reason behind using a servo is that it provides angular precision, i.e. it will only rotate as much we want and then stop and wait for next signal to take further action. This is unlike a normal electrical motor which starts rotating as and when power is applied to it and the rotation continues until we switch off the power.
Few images during developments:
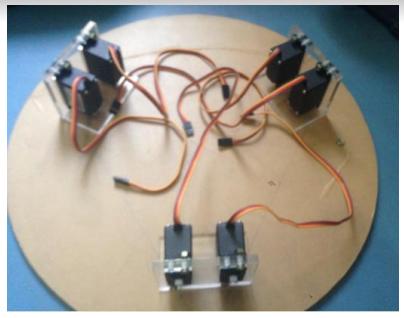
.png)
Motors are attached as shown in above figure. Below figure shows movements in z+, y- and y+ respectively.
.png)
Six servo motors are connected with Arduino with six PWM pins. For different movement different duty cycle pulses are generated on each PWM pin.
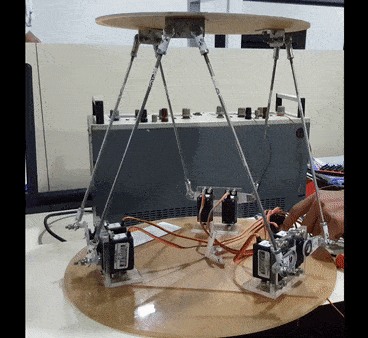