With new IoT sensor technology available, manufacturers have access to an ever-increasing variety of devices that can help them better manage and enhance their manufacturing process. These include machines that can locate and predict machinery failures and others that can report on inventory levels or control the quality of products.
What Are IoT Sensors?
An IoT sensor is a device that can uniquely identify its location, capture data about the environment in which it exists, and transmit that data for further analysis by a network of computers.
This combination of capabilities enables manufacturers to collect relevant information about the performance of critical assets and processes, enabling them to make better decisions based on real-time monitoring. The combination of sensors and data analytics also allows manufacturers to predict problems before they occur and optimize their supply chains for greater efficiency.
IoT Testing in Manufacturing
Manufacturers are using IoT sensors to monitor their production lines, improve efficiencies, decrease downtime and increase profitability. In a manufacturing setting, IoT sensors are connected directly to the machinery they monitor. They can also be attached to other assets, including hoses, tools, and containers, where they gather the information that is used by computer systems to drive production processes. Yalantis is a great resource for all manufacturers seeking to improve their processes with IoT testing.
The following are examples of how manufacturers use internet of things sensors to monitor and optimize the performance of their machinery.
1. Predicting Failures
A predictive maintenance platform can monitor the temperature, vibration, and other signals that indicate potential problems in a manufacturing process. It can then automatically send signals to a system operator or machine controller when it detects a potential problem. This allows the machine to be taken down for repair or replacement before an actual failure occurs, saving valuable time and preventing unscheduled downtime.
2. Monitoring Machine Performance
Industrial IoT sensors allow manufacturers to measure tangible data about specific machines during operation, making it possible to measure the machine's performance over time. This can help manufacturers lower costs and improve efficiencies by detecting an increase in wear and tear that could indicate a need for replacement.
3. Monitoring Inventory Levels
Automated inventory management systems can transmit real-time data to a computer system designed to monitor and predict the number of parts on hand. The results are transmitted to the machine controller and can help to optimize production schedules.
4. Safety Monitoring
IoT sensors designed specifically for use in manufacturing are fixed to assets where they measure vibration levels, pressure, temperature, and other factors that indicate potential safety issues. When abnormal levels are detected, activity on the assembly line can be stopped until further investigation takes place.
5. Logistics Monitoring
IoT sensors can be placed on pallets, trucks, loading docks, or anywhere else in the supply chain to track movement. They provide real-time data that can troubleshoot delays or problems with a shipment and trigger alerts if the shipment is approaching its delivery deadline.
Benefits of IoT Sensors
1. Newer Sensors Are More Compact and Versatile
Newer sensors can be small enough to be embedded into a plastic part, so manufacturers can place them in locations where they'll have the best results. They also sync wirelessly, so there's no need for attachment through cables or wires. Finally, they use less energy than older sensors, which means they can run on smaller batteries.
2. New Sensors Offer Greater Accuracy
Newer sensors read with greater accuracy than older models. An accelerometer, for example, can detect a wider range of movement. As a result, it can be placed at key points on machines or products to provide a greater level of detail about potential problems.
3. New Sensor Technology Offers Increased Data Collection
New sensors collect and analyze more data than older models. Because they're connected to the Internet, the information they provide is more accessible and allows manufacturers to monitor their entire production process – not just specific machines or lines – which enables greater efficiency and accuracy overall.
4. New Sensors Enable Better Insights Into Customer Needs
Manufacturers can use smart devices to collect data on a wider range of parameters, including those that could indicate problems with their machines. By collecting this data and analyzing it on a larger scale, manufacturers can better understand how their customers use their products, which helps them create products that appeal to customers more effectively.
5. New Sensors Allow Manufacturers To Improve Product Quality
Manufacturers can use new sensors to detect problems before they can cause damage or negatively affect quality. They also report on the conditions that caused issues and suggest ways to prevent similar problems in the future.
IoT Sensors in Manufacturing: Challenges and Opportunities
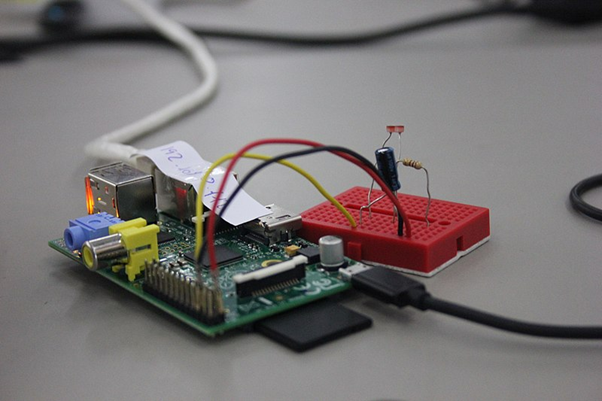
While IoT sensors have many benefits for manufacturers, they also have some drawbacks. Because sensors are small and easily overlooked, it can be difficult to verify their security and confirm that they are transmitting data accurately. This can result in inaccurate information or a loss of valuable data if the connection is broken.
Another challenge is the sheer number of IoT systems that manufacturers must connect to their production environment. While a single sensor may be simple to install, connecting it to the many systems it will have to interact with requires an understanding of the design and architecture and strong technical skills in computer programming.
How To Choose IoT Sensors for Manufacturing Use
One of the most important considerations when deciding which IoT sensors to use in manufacturing is to determine how you intend to use the data provided by the sensors. This will help you decide on features you need, such as battery life.
Another important factor to consider is security. In an industrial environment, there must be a high level of assurance that data is being transmitted securely and accurately between sensors and the network.
You should consult different sensor manufacturers for internet of things and professional software developers before selecting a device for use in manufacturing. This is because different sensors perform functions that fall under several categories.